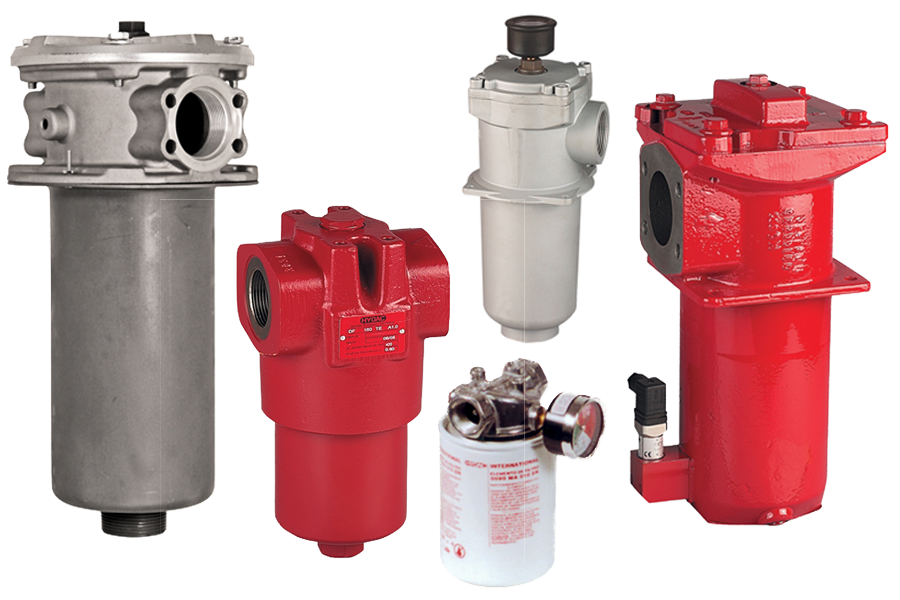
“Choosing the right hydraulic filter requires careful evaluation of various factors…”
For more details, please contact us:
Phone: (971) 264-0400
In hydraulic systems, the efficiency and longevity of the components heavily depends upon the cleanliness of the hydraulic fluid. Contaminants such as dirt, debris, and particles can cause significant damage to sensitive hydraulic components, leading to reduced performance and increased maintenance costs. Hydraulic filters play a crucial role in maintaining the cleanliness of the fluid by removing these contaminants. This blog post aims to provide comprehensive insights into hydraulic filter design, construction, ratings, specifications, and materials. By understanding the intricacies of hydraulic filter selection, professionals can make informed decisions to ensure optimal filtration and system performance.
I. Hydraulic Filter Design:
Hydraulic filters are designed to capture and retain contaminants of various sizes. The primary components of a hydraulic filter include the filter media, housing, bypass valve, seals, and end caps. The filter media is the heart of the filter, responsible for separating contaminants from the hydraulic fluid. It is typically made of synthetic fibers, metal mesh, or a combination of both. The filter media’s design, thickness, and density are critical factors influencing the filter’s efficiency and dirt-holding capacity.
II. Hydraulic Filter Construction:
Hydraulic filters are available in different configurations, including inline, cartridge, spin-on, and tank-mounted filters. Inline filters are installed directly into the hydraulic line, while cartridge filters consist of a replaceable element housed in a metal or plastic casing. Spin-on filters feature a self-contained design that allows for quick and easy replacement. Tank-mounted filters are submerged in the hydraulic reservoir, providing continuous filtration.
III. Hydraulic Filter Ratings:
Hydraulic filters are rated based on their ability to capture and retain contaminants. The most common rating systems include the Beta Ratio (β), Micron Rating (µ), and ISO Cleanliness Code. The Beta Ratio indicates the filter’s efficiency in removing particles of a particular size. A higher Beta Ratio signifies better filtration performance. The Micron Rating refers to the size of particles the filter can effectively capture. A lower micron rating corresponds to a finer level of filtration. The ISO Cleanliness Code classifies the cleanliness level of the hydraulic fluid before and after filtration.
IV. Hydraulic Filter Specifications:
Selecting the appropriate hydraulic filter requires careful consideration of system requirements and specifications. Factors such as flow rate, pressure rating, and compatibility with hydraulic fluids must be evaluated. The flow rate determines the filter’s size and capacity to handle the fluid flow without causing excessive pressure drop (ΔP). Pressure ratings ensure that the filter can withstand the operating pressure of the hydraulic system. Compatibility with hydraulic fluids, including mineral oils, synthetic fluids, and biodegradable fluids, is essential to prevent degradation or failure of the filter.
V. Hydraulic Filter Materials:
Hydraulic filters are constructed using a variety of materials, each offering specific advantages and limitations. Filter housings are commonly made of aluminum, steel, or plastic, depending on the application and environmental conditions. Aluminum provides excellent strength-to-weight ratio, while steel offers durability and resistance to high-pressure applications. Plastic housings are lightweight and resistant to corrosion. The filter media can be composed of cellulose, synthetic fibers, wire mesh, or metal screens. Cellulose filters are cost-effective but have limited temperature and chemical resistance. Synthetic filters are more efficient, durable, and suitable for a wider range of operating conditions. Wire mesh and metal screens are commonly used as pre-filters to protect finer filter media.
VI. Challenges in Choosing a Proper Hydraulic Filter:
While the selection of a hydraulic filter may seem straightforward, there are several challenges that professionals must address to ensure the filter’s effectiveness and compatibility with the hydraulic system. The following factors should be carefully considered:
- Fluid Viscosity: The viscosity of the hydraulic fluid plays a crucial role in filter selection. High-viscosity fluids require filters with larger surface areas and coarser filter media to prevent excessive pressure drops. Conversely, low-viscosity fluids necessitate filters with finer media to capture smaller contaminants effectively.
- Temperature Range: Hydraulic systems operate within a wide range of temperatures, and the filter must be capable of handling these extremes. Filters should be selected based on their ability to maintain adequate filtration efficiency and structural integrity under high and low temperature conditions. Heat-resistant materials and designs with bypass valves to prevent cold-start damage are also considerations in such cases.
- Pressure Fluctuations: Hydraulic systems often experience pressure fluctuations during normal operation or due to system demands. Filters must be selected to withstand these fluctuations without compromising their integrity. High-pressure spikes or pulsations may require filters with reinforced housings or additional support to prevent failure.
- Contamination Levels: Understanding the expected contamination levels in the hydraulic system is crucial for filter selection. Factors such as the operating environment, system design, and maintenance practices influence the contamination levels. Filters should have an appropriate Beta ratio and micron rating to effectively capture contaminants of the expected size range.
- Water and Moisture: Hydraulic systems may be exposed to water or moisture ingress, which can lead to fluid degradation, component damage, and increased wear. Filters with water-absorbing media or coalescing filters that separate water from the fluid can be used to mitigate these issues. Additionally, regular monitoring and maintenance practices should be implemented to address water-related concerns.
- Compatibility with Hydraulic Fluids: Hydraulic systems use different types of fluids, including mineral oils, synthetic fluids, and biodegradable fluids. Filters must be compatible with the specific fluid being used to avoid chemical degradation, reduced filtration efficiency, or leaks. Manufacturers’ recommendations and compatibility charts should be consulted to ensure proper filter selection.
- Service Life and Maintenance: Determining the desired service life of the filter and establishing a maintenance schedule are essential for system performance and cost-effectiveness. Filters with high dirt-holding capacities may have longer service intervals but can increase pressure drop and affect system efficiency. Regular monitoring of pressure differentials across the filter and following manufacturer guidelines for filter replacement are crucial to maintain optimal filtration performance.
- Size and Installation Constraints: Hydraulic systems often have space limitations, requiring filters to be compact and easily installed. Consideration should be given to the filter’s dimensions, mounting options, and accessibility for replacement or maintenance.
Conclusion:
Choosing the right hydraulic filter requires careful evaluation of various factors, including fluid viscosity, temperature range, pressure fluctuations, expected contamination levels, water and moisture concerns, compatibility with hydraulic fluids, service life, and installation constraints. By addressing these challenges and selecting filters that meet system requirements, professionals can ensure effective filtration, reduce maintenance costs, and extend the life of hydraulic components. Hydraulic training should emphasize the importance of proper filter selection and maintenance practices to optimize system performance and reliability.
Hydraulic training should emphasize the importance of proper filter selection and maintenance practices to optimize system performance and reliability.