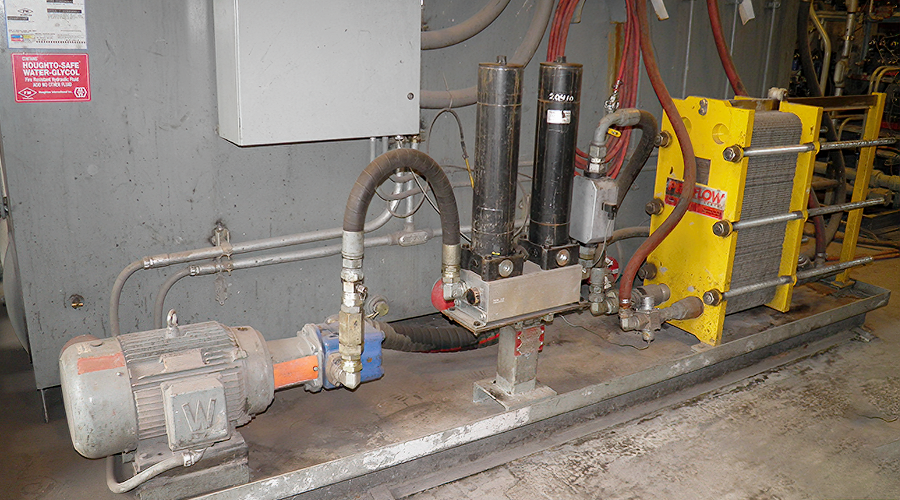
Fluid contamination is one of the most significant factors impacting the overall performance and lifespan of a hydraulic system.
For more details, please contact us:
Phone: (971) 264-0400
Hydraulic systems are used in various industrial applications, such as manufacturing, construction, and transportation, to transmit power using pressurized fluids. One of the primary factors that can impact performance and lifespan of a hydraulic system is fluid contamination. In this article, we will discuss the different types of hydraulic fluid contaminants, their effects on system performance, and various strategies for contamination control.
Types of Hydraulic Fluid Contaminants:
Hydraulic fluids can become contaminated by various means, including air, water, and particulate matter. The different types of hydraulic fluid contaminants include:
- Air Contamination: When air enters the hydraulic fluid, it can cause the formation of bubbles, leading to cavitation and reduced fluid performance. Air can also lead to oxidation of the fluid, which can cause the formation of sludge and varnish.
- Water Contamination: When water enters the hydraulic system, it can cause fluid degradation, corrosion, and damage to components. Water can enter the system through leaks, condensation, or the introduction of contaminated fluid.
- Particulate Matter Contamination: This includes dirt, dust, metal shavings, and other debris that enter the hydraulic fluid during operation. Particulate matter causes wear and damage to components, leading to decreased system performance and lifespan.
Effects of Fluid Contamination on Hydraulic Systems:
Fluid contamination can have several adverse effects on hydraulic system performance, including:
- Reduced Component Life: Contaminated hydraulic fluid can cause damage and wear to components such as pumps, valves, and cylinders, leading to reduced lifespan and increased maintenance costs.
- Reduced System Performance: Contaminated hydraulic fluid can lead to decreased system performance, reduced power output, slower operation, and increased energy consumption.
- System Failure: Severe fluid contamination can cause catastrophic system failure, resulting in safety risks, costly repairs, and unscheduled downtime.
Contamination Control Strategies:
There are several strategies for successfully controlling hydraulic fluid contamination, including:
- Proper Fluid Selection: Choosing the right hydraulic fluid for the specific application is critical for maintaining system performance and preventing contamination. The fluid should meet the system’s specific requirements regarding viscosity, oxidation stability, and resistance to water and air contamination.
- Regular Fluid Analysis: Regular fluid analysis can help identify contamination issues before they cause significant damage. Analysis should include particle counts, water content, and viscosity measurements.
- Installation of Filtration Systems: The installation of appropriate filtration systems, such as magnetic, bag, or cartridge filters, can help remove particulate matter from the hydraulic fluid. The filters should be appropriately sized and located to ensure effective filtration.
- Preventative Maintenance: Regular preventative maintenance, including component inspections, fluid changes, and system flushing, can help prevent contamination and ensure proper system operation.
- Proper Storage and Handling: Proper storage and handling of hydraulic fluids can prevent contamination from air, water, and particulate matter. Fluids should be stored in a clean, dry, and temperature-controlled environment and handled using clean tools and equipment.
- Education and Training: Proper education and training of personnel involved in hydraulic system operation and maintenance can help prevent contamination. Training should include best practices for fluid selection, filtration, handling, and maintenance.
Conclusion:
Fluid contamination is a significant challenge that can impact hydraulic system performance, lifespan, and safety. Proper contamination control strategies, including proper fluid selection, regular fluid analysis, installation of filtration systems, preventative maintenance, proper storage and handling, and education and training, can all help to prevent contamination and ensure proper system operation. By implementing these strategies, hydraulic system personnel can prevent costly system failure and ensure that their systems operate at peak performance levels.
New oil is NOT clean oil!
Always fill reservoirs through a filter.